IB Business Management
Unit 5.2 Operations Methods
Case Study: Time to change for Horologix?
In the boardroom of Horologix Co., an artisanal watchmaker, a key decision is coming. Famous for high quality craftsmanship, Horologix now struggles with whether to shift from batch production to mass production!
The business operates as a private limited company (Ltd) and is family run. Some of the four board members feel that Horologix has grown to its maximum size offering batch produced, relatively high-priced watches!
The surge in demand for its watches prompts a strategic assessment. The surge has continued for two years now. However, the big boost came recently from free online marketing and helpful promotion by a popular online influencers who said that,
“These watches are absolute must haves; nobody makes stuff like this anymore”!
This comment was shared online and seen millions of times over a short period! Orders came in quickly and stocks of watches sold out!
Mass production offers efficiency through economies of scale. This could allow a broader market and greater sales and higher profits (says one board member).
On the flip side, the merits of batch production lie in their artisanal charm (says another board member). We don’t want to ruin what made us successful!
Whilst board members disagree, they all want to take advantage of their growing popularity and generate increased profit. Profit is something they agree upon! One potential problem is that mass produced (anything) is against the beliefs of one of the board members. They consider that mass production is wasteful and doesn’t respect natural resources! Also, they say,
“being somewhat sustainable has helped us to develop brand loyalty and a good name in the market. We go mass, we undermine and go against the trend”!
The boardroom meeting analyses the following proposals!
- Maintain Horologix using batch production and seek to reduce costs to improve profit and expand slowly.
- Switch to mass production and significantly increase the output whilst seeking to sell in new markets.
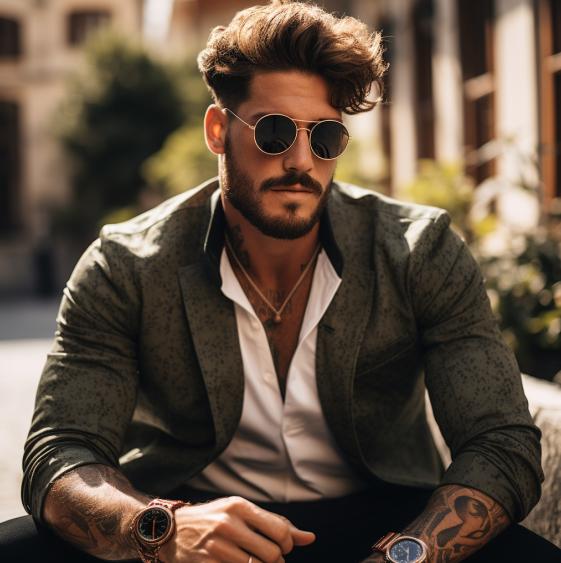
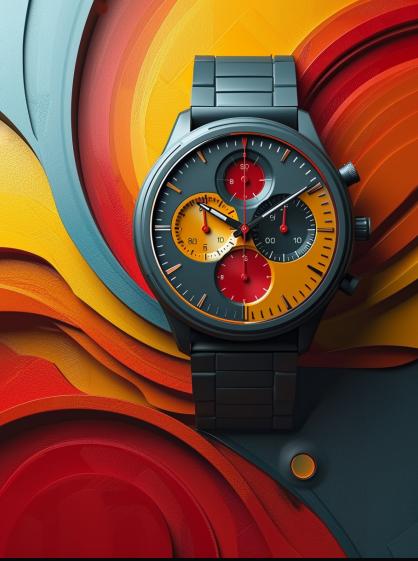
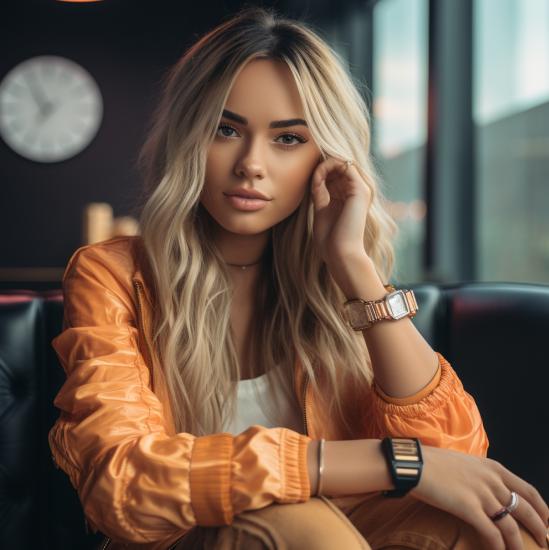
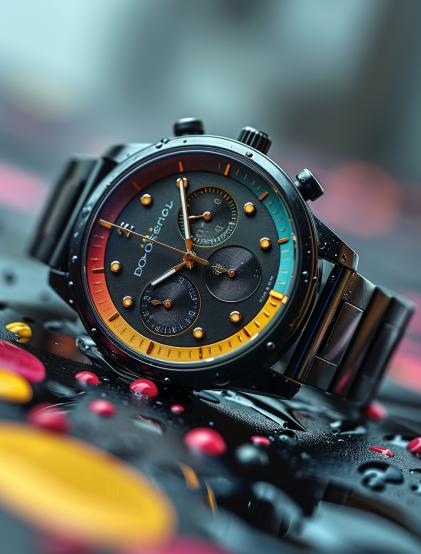
Key terms
QUESTIONS FROM THE HOROLOGIX CASE STUDY
- Define (with reference to the case study) the term, sustainability [2]
- Define a private limited company LTD [2]
- Suggest (with reference to the case) how added value may be affected when changing to mass produced watches [2]
- Define the term economies of scale [2]
- Explain (with reference to the case) two potential economies of scale that Horlogix could benefit from if they switch to mass production [4]
- Discuss whether Horologix should choose Option one or option two [10]
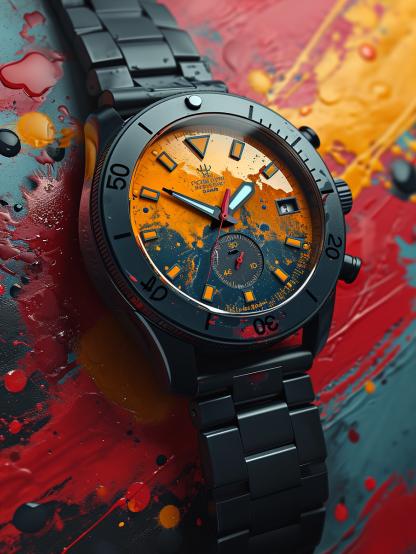
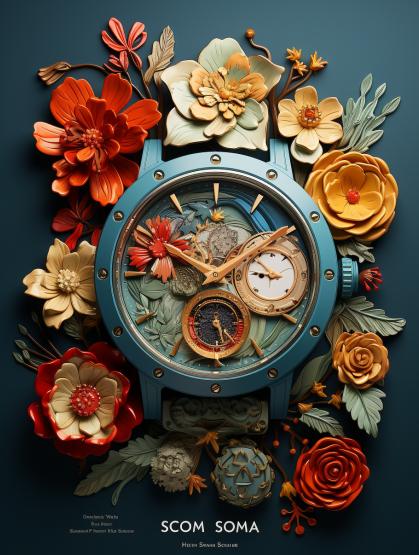
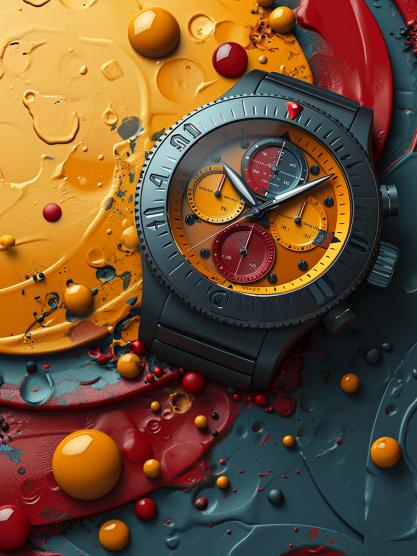
Production methods overview
In job production, also known as custom or bespoke production, each product is uniquely designed and produced to meet the specific requirements of a customer. This approach is common in industries where customization and personalization are key. Let’s explore some advantages and disadvantages of job production:
Advantages:
Customization: Job production allows for high levels of customization. Each product can be tailored to meet the unique needs and preferences of individual customers, leading to increased customer satisfaction.
Quality Control: Since each product is produced separately, there is greater opportunity for quality control and attention to detail. Manufacturers can closely monitor the production process and ensure that each item meets high-quality standards.
Flexibility: Job production is highly flexible, making it suitable for businesses dealing with a wide variety of products or those responding to diverse customer demands. It can easily adapt to changes in design or specifications.
Skill Utilization: Job production often involves skilled labor, and this method allows for the utilization of specialized skills. Craftsmanship and attention to detail are valued, contributing to the creation of high-quality products.
Disadvantages:
Costs: Job production can be expensive due to the need for skilled labor, customization, and setup costs for each unique order. This may result in higher per-unit costs compared to mass production methods.
Time-Consuming: The production process for each job is time-consuming, and lead times can be longer. This might not be suitable for businesses that require quick turnaround times or operate in fast-paced markets.
Economies of Scale: Job production may not benefit from economies of scale as larger production runs typically result in lower per-unit costs. This can make it challenging to compete on price with mass production methods.
Resource Allocation: Since each job is unique, resource allocation can be complex. Balancing the availability of skilled labor, materials, and production capacity for different jobs can be a logistical challenge.
Job production is a strategic choice for businesses aiming to provide highly customized and unique products
In the batch production method, goods are produced in specific quantities or batches before moving on to the next set. This approach allows for flexibility in adjusting production based on demand or changes in design. Let’s delve into some advantages and disadvantages:
Advantages:
Flexibility: Batch production offers flexibility as it allows for changes in the production process or product design between batches. This is beneficial for businesses dealing with varying customer demands.
Efficiency: It can be more efficient than one-off production methods since equipment can be set up to produce a specific batch, and then reconfigured for the next. This reduces downtime and enhances overall efficiency.
Quality Control: With batch production, it’s easier to implement quality control measures as each batch can be thoroughly inspected before the next one begins. This helps in maintaining consistent product quality.
Disadvantages:
Cost: Setting up and reconfiguring equipment for each batch incurs costs. The downtime between batches can also lead to increased idle time, impacting overall production costs.
Time-Consuming: The process can be time-consuming, especially if the setup and reconfiguration of equipment take a significant amount of time. This may result in longer lead times for fulfilling orders.
Inventory Management: Batch production may lead to higher levels of work-in-progress inventory since multiple batches are in various stages of production simultaneously. This ties up capital and storage space.
Less Economies of Scale: Batch production may not benefit as much from economies of scale as continuous production methods. Larger quantities often result in lower per-unit costs, which may not be fully realized in batch production.
Understanding the dynamics of batch production is crucial for businesses aiming to balance efficiency and flexibility in their production processes.
In mass or flow production, large quantities of standardized products are produced in a continuous and efficient process. This method is characterized by the use of assembly lines and automated machinery. Let’s look at some key points based on the IB Business Management syllabus:
Advantages:
Economies of Scale: Mass production benefits from economies of scale, resulting in lower average costs per unit. The high volume of production allows businesses to take advantage of bulk purchasing, specialized machinery, and efficient processes.
Consistency and Standardization: The standardized nature of mass production ensures consistency in product quality and specifications. This is crucial for meeting customer expectations and building a strong brand reputation.
Efficiency: Mass production is highly efficient as it minimizes downtime and utilizes automated processes. This leads to increased productivity and faster production cycles, allowing businesses to respond to market demands more effectively.
Lower Labor Costs: Automation and specialization in mass production often lead to lower labor costs per unit. This contributes to the overall cost-effectiveness of the production process.
Disadvantages:
Lack of Flexibility: Mass production is less flexible compared to other production methods. The setup for a specific product may require significant time and resources, making it challenging to adapt quickly to changes in consumer preferences or market demands.
Boredom and Fatigue: Workers in mass production settings may experience boredom and fatigue due to repetitive tasks on the assembly line. This can lead to decreased motivation, increased absenteeism, and potential quality issues.
High Initial Capital Investment: The setup of mass production facilities involves a substantial initial capital investment in specialized machinery and infrastructure. This can be a barrier for smaller businesses or startups.
Dependence on Forecasting: Mass production relies heavily on accurate demand forecasting. Inaccurate predictions can lead to overproduction or underproduction, impacting inventory levels and overall efficiency.
Mass customization is a production method that combines elements of mass production and customization to meet the unique needs of individual customers. Here’s an overview of mass customization based on the IB Business Management syllabus:
Advantages:
Customer Satisfaction: Mass customization allows businesses to offer products that meet the specific preferences and requirements of individual customers. This enhances customer satisfaction and loyalty by providing a personalized experience.
Flexibility: Unlike traditional mass production, mass customization offers a degree of flexibility in adapting to diverse customer demands. This allows businesses to respond to changing market trends and individual preferences more effectively.
Economies of Scope: Mass customization aims to achieve economies of scope, where a variety of customized products can be produced using shared resources and processes. This helps in optimizing production efficiency and cost-effectiveness.
Enhanced Brand Loyalty: Providing customized products can create a strong emotional connection with customers, leading to increased brand loyalty. Customers are more likely to remain loyal to a brand that caters to their unique preferences.
Disadvantages:
Complexity in Production: Implementing mass customization requires sophisticated production processes and technologies. Managing the complexity of producing a wide range of customized products can be challenging and may require significant investment.
Higher Costs: The level of customization in mass customization can lead to higher production costs compared to more standardized production methods. This is due to the need for flexible production processes and specialized technologies.
Potential for Over-Engineering: In an effort to meet specific customer demands, there is a risk of over-engineering products, resulting in unnecessary complexity and higher costs. Balancing customization with cost-effectiveness is crucial.
Demand Forecasting Challenges: Mass customization relies on accurate demand forecasting to efficiently manage resources and production schedules. Unpredictable or fluctuating demand can pose challenges in maintaining an optimal balance between customization and efficiency.
These key points cover the basics of mass customization in the context of the IB Business Management syllabus, emphasizing customer satisfaction, flexibility, economies of scope, and potential challenges related to production complexity and cost considerations.
KEY TERMS FROM THE HOROLOGIX CASE STUDY
SUGGESTED ANSWERS TO THE HOROLOGIX CASE STUDY QUESTIONS
- Define the term, sustainability [2]
Sustainability refers to the ability of a business or organization to meet its current needs and operations without compromising the ability of future generations to meet their own needs. It involves adopting practices that are environmentally responsible, socially equitable, and economically viable in the long term.
- Define a private limited company [2]
A private limited company is a type of business structure that is privately held and limits the liability of its owners (shareholders). It restricts the number of shareholders, and shares are not publicly traded. The company’s shares are held by a select group of individuals, often family members or a small group of investors.
- Suggest how added value may be affected when changing to mass-produced watches [2]
When transitioning to mass production, added value in artisanal watches may decrease due to the standardization of the manufacturing process. The uniqueness and craftsmanship associated with artisanal production may be compromised, potentially reducing the perceived value of the watches in the eyes of consumers.
- Define the term economies of scale
Economies of scale refer to the cost advantages that a business can achieve when it produces goods or services on a larger scale. As the volume of production increases, the average cost per unit decreases, leading to increased efficiency and potentially higher profit margins.
- Explain two potential economies of scale that could be used when switching from batch to mass production
a. Technical Economies: Mass production allows for the utilization of specialized machinery and technology, reducing the cost per unit by increasing efficiency and output.
b. Managerial Economies: With increased production volume, managerial functions can be streamlined, leading to more efficient coordination, planning, and decision-making, thereby reducing per-unit costs.
- Discuss whether Horologix should choose Option one or option two [10]
The decision between batch production and mass production at Horologix involves weighing the merits of artisanal charm against the efficiency and potential for increased profits through economies of scale.
Option One (Batch Production):
- Strengths:
- Maintains artisanal charm and uniqueness.
- Aligns with sustainability values, fostering brand loyalty.
- Weaknesses:
- Limits production volume, potentially hindering market expansion.
- May not fully capitalize on the recent surge in demand.
Option Two (Mass Production):
- Strengths:
- Leverages economies of scale for efficiency and cost reduction.
- Opens doors to a broader market, increasing potential sales and profits.
- Weaknesses:
- Risks compromising artisanal charm, potentially alienating loyal customers.
- Goes against the sustainability values of one board member.
Recommendation: Considering the surge in demand and the potential for increased profits, a hybrid approach could be explored. Implementing selective mass production for certain models while maintaining a limited batch production for unique designs could strike a balance between efficiency and artisanal charm. This approach would cater to both the growing market demand and the values of sustainability, ultimately maximizing overall profitability. Communication strategies should also emphasize the commitment to sustainable practices to maintain brand loyalty and market reputation.
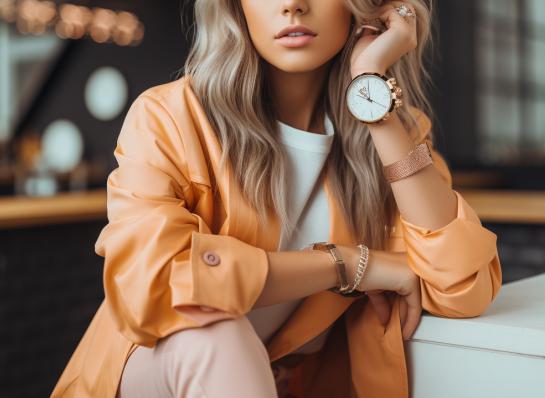
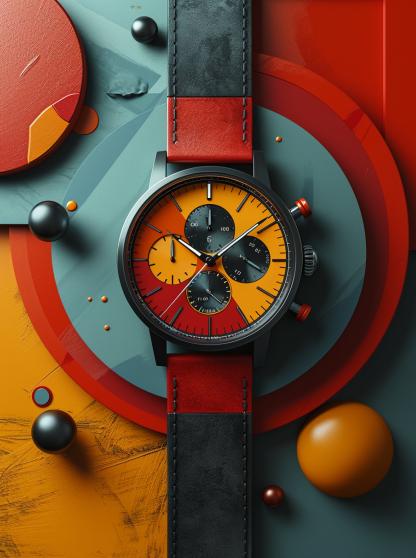
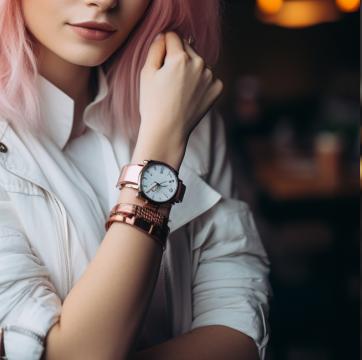